In the label industry, a spectrum of release liner materials and specialized equipment are crucial. Each material serves unique functions in application and manufacturing, contributing to their usage across the label sector.
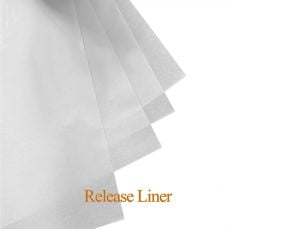
Machinery is the first consideration. Release liner production requires machines equipped with coating and calendering capabilities.
Calendering involves passing paper through alternating stacks of rollers that apply pressure, heat, and friction to smooth and polish the material. Supercalendering takes this a step further, utilizing additional calenders to produce an even smoother, more glossy surface.
While various release liner materials exist, we’ll focus on three primary types that use paper:
- CCK (Clay Coated Kraft): The most economical option, CCK is essentially clay-coated paper. It has the lowest density and opacity among the three, lying flat due to its low flexibility. These properties make CCK suitable for graphics or laser labels.
- SCK (Super Calendered Kraft): Predominantly used in North America, SCK is common in thermal transfer label printing and application. While CCK derives its barrier properties (against silicone) from its clay coating, SCK achieves its barrier properties and low opacity through higher density. SCK production in the US is typically completed in a single manufacturing operation.
- Glassine: The most expensive of the three, glassine requires additional production steps. It undergoes 2-3 manufacturing operations, including rewetting and recalendering. This results in a thinner yet highly durable material with the highest density and lowest opacity, distinguishing glassine from other release liners.