The manufacturing of silicone coated release liners involves several key steps to ensure that the final product meets industry standards for performance and quality. Below is a detailed overview of the manufacturing process:
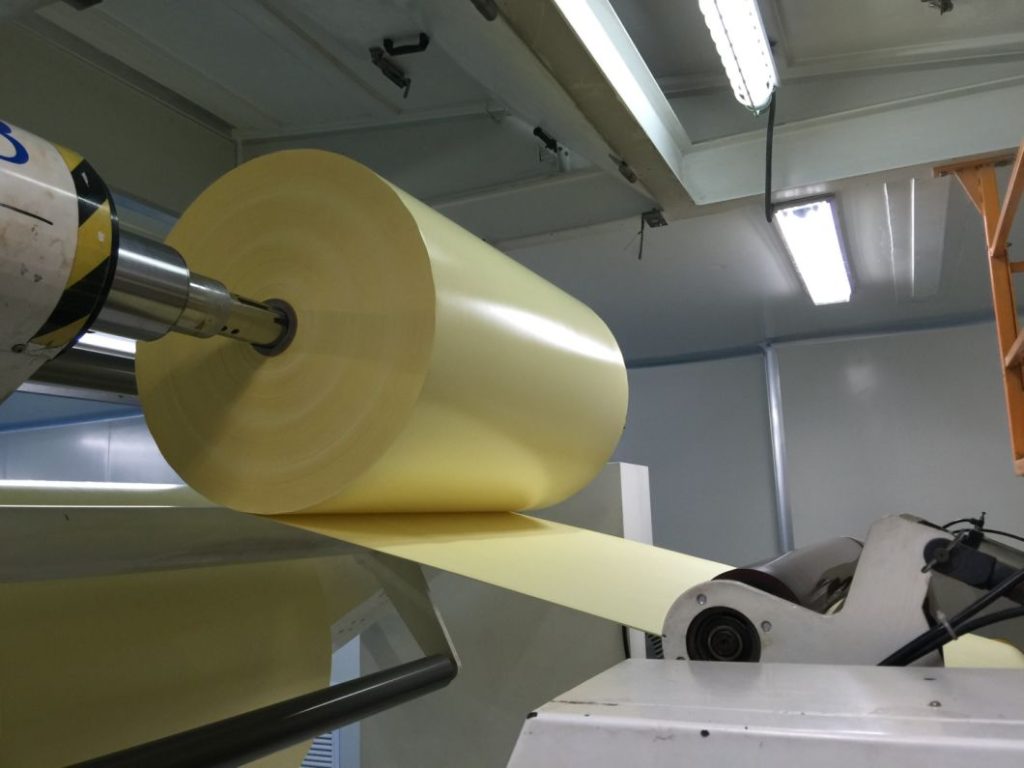
1. Material Selection
The first step in manufacturing silicone coated release liners is selecting the appropriate substrate material. Common substrates include:
- Paper: Typically coated or uncoated paper.
- Film: Various plastic films, such as polyethylene (PE) or polyester (PET), are also used.
The choice of substrate depends on the intended application and desired properties.
2. Surface Preparation
Before applying the silicone coating, the substrate must undergo surface preparation. This can involve:
- Cleaning: Removing impurities, dust, or oils that could affect adhesion.
- Priming: In some cases, a primer may be applied to enhance the bond between the substrate and the silicone coating.
3. Silicone Coating Application
The silicone coating is applied using one of several methods, including:
- Gravure Coating: This method uses engraved cylinders to transfer a precise amount of silicone onto the substrate.
- Slot Die Coating: A slot die applies a uniform layer of silicone across the substrate width.
- Roll Coating: In this method, a roller applies the silicone to the substrate as it passes through.
The choice of application method affects the coating thickness and uniformity.
4. Curing Process
After the silicone is applied, the coating must be cured to achieve its final properties. Common curing methods include:
- Heat Curing: The coated substrate is passed through an oven to cure the silicone, allowing it to bond effectively to the substrate.
- UV Curing: Ultraviolet light is used to cure the silicone, providing a faster curing process.
Curing is critical for developing the non-stick properties and durability of the release liner.
5. Quality Control
Throughout the manufacturing process, quality control measures are implemented to ensure that the liners meet specifications. This includes:
- Thickness Measurement: Ensuring the silicone layer is uniform and meets required thickness.
- Adhesion Testing: Verifying that the silicone coating adheres properly to the substrate and performs as expected during release applications.
- Visual Inspection: Checking for any defects or inconsistencies in the coating.
6. Cutting and Finishing
Once cured and tested, the silicone coated release liners are cut to the desired sizes. This can involve:
- Slitting: Cutting the large rolls into smaller rolls or sheets.
- Finishing: Additional processes, such as applying protective liners or packaging, may be performed.
7. Packaging and Distribution
Finally, the finished silicone coated release liners are packaged for distribution. Proper packaging is essential to protect the liners from damage during transport and storage.